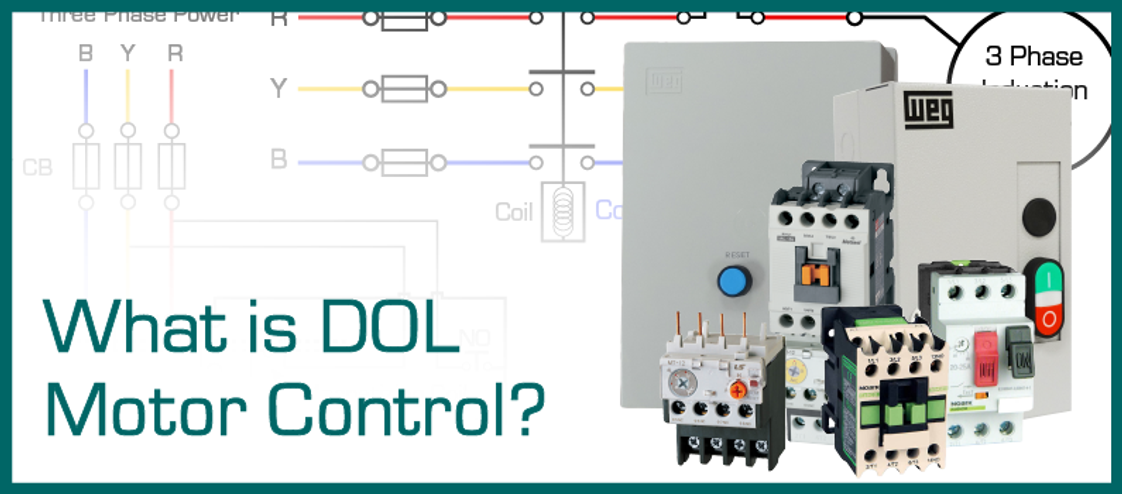
What is Direct on Line (DOL) Motor Control?
Posted by Morgan Spano on Apr 21st 2022
Considered the most simple motor start option, Direct on Line (DOL) starting directly connects an induction motor to a 3-Ph power supply with the addition of a contactor and an overload relay, providing overload protection.
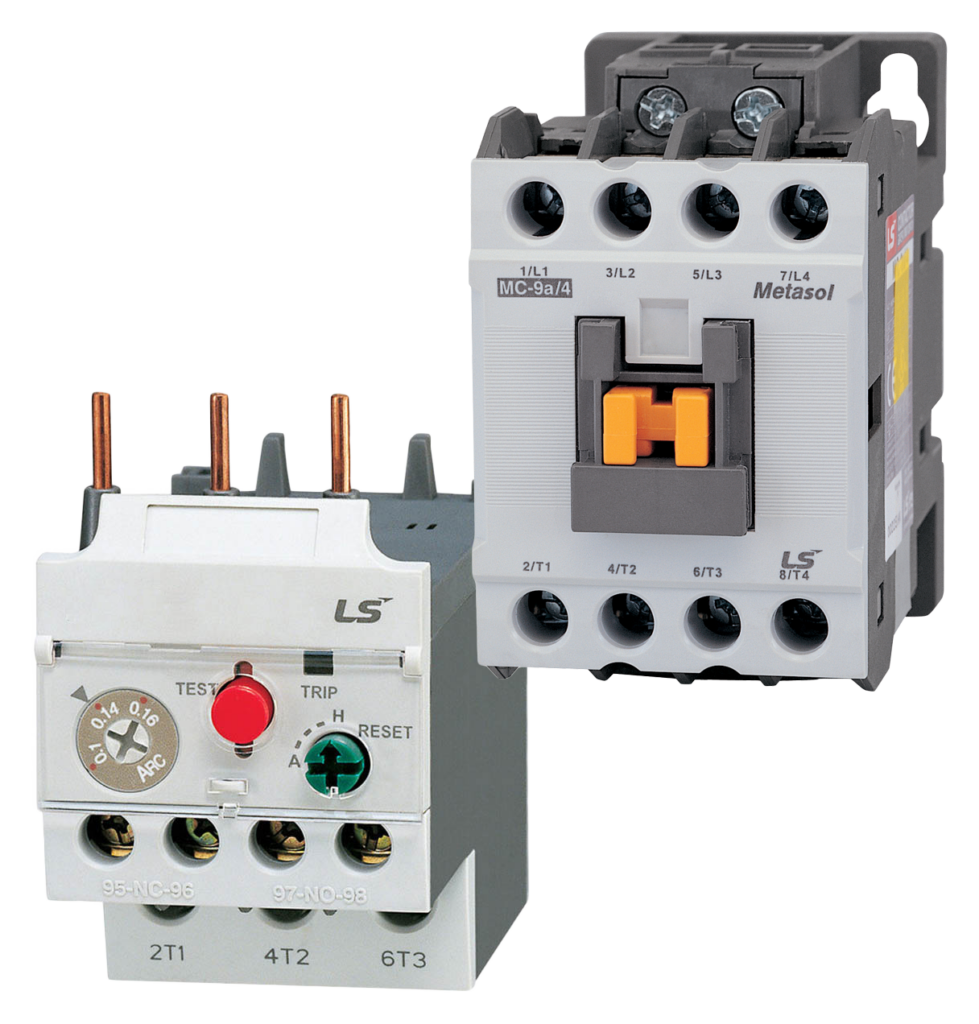
This direct connection can cause the motor to draw 5-8 times the normal operating current, making DOL motor control generally applicable with motors under 5 hp/4Kw.
Imagine opening the floodgates up all at once, it’s better to work with something smaller and more manageable rather than something huge and catastrophic.
Essentially, a DOL starter is comprised of some form of contactor and an overload protector which turns the motor ON or OFF. How these two are included in your project depends more on the application requirements.
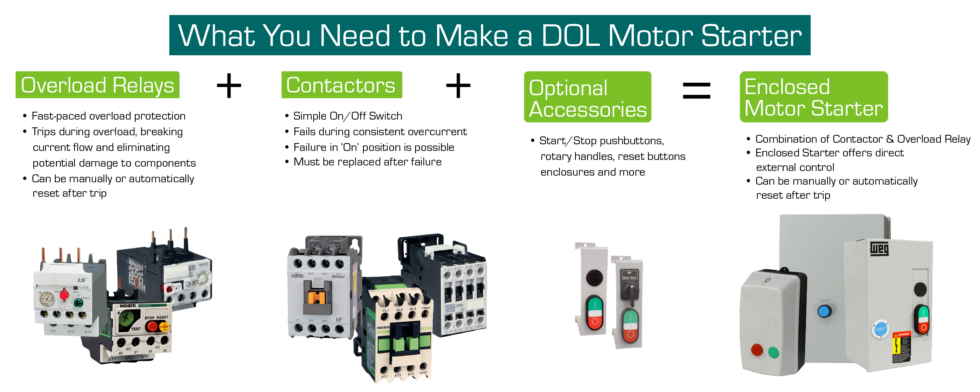
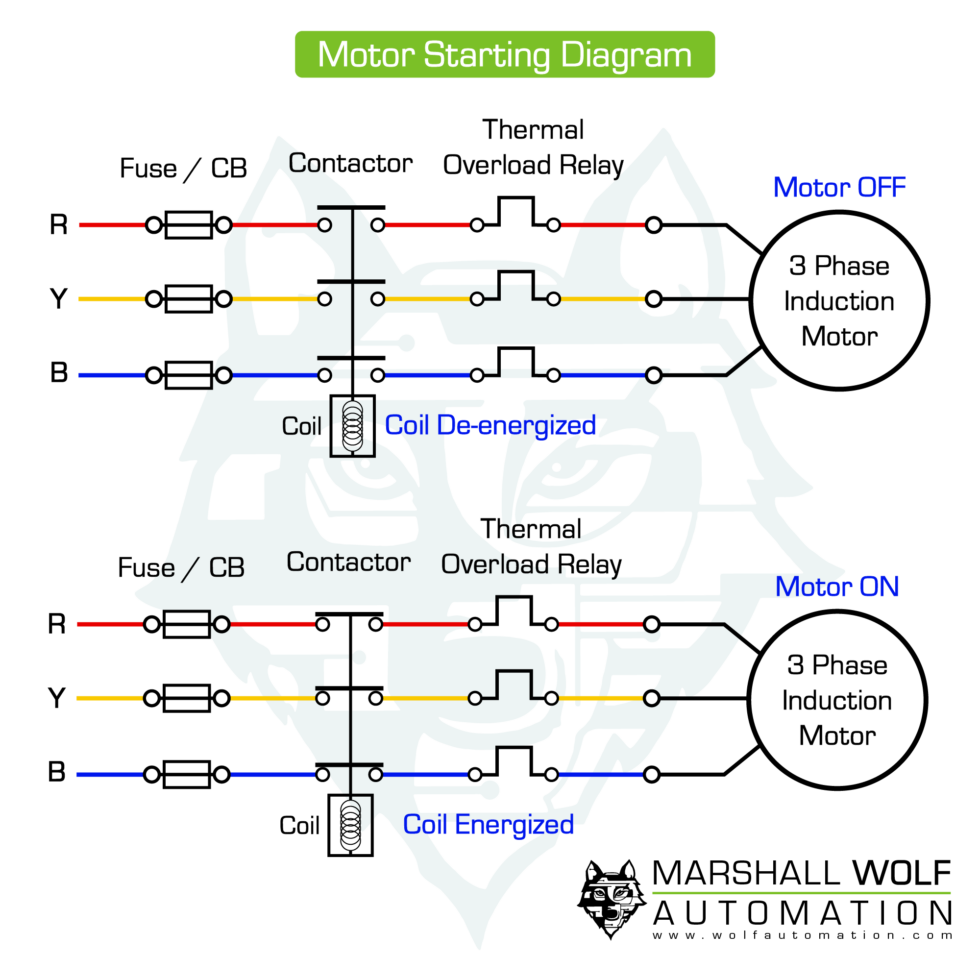
With DOL, controlling your motor is as easy as on and off. Contactors are simple devices which generally have three main NO (normally open) contacts and an auxiliary contact (NO/NC).
The three main contacts are used to connect the motor to the supply lines while the auxiliary contact acts as the control circuit, energizing the magnetizing coil after the start button is pressed. If the contactor detects current overload, it breaks the circuit de-energizing the motor.
Tripping the contactor may be a handy way to protect your motor in extreme cases, but the drawback is the fact they can fail in the ON position and likely will need replacing after a current overload.
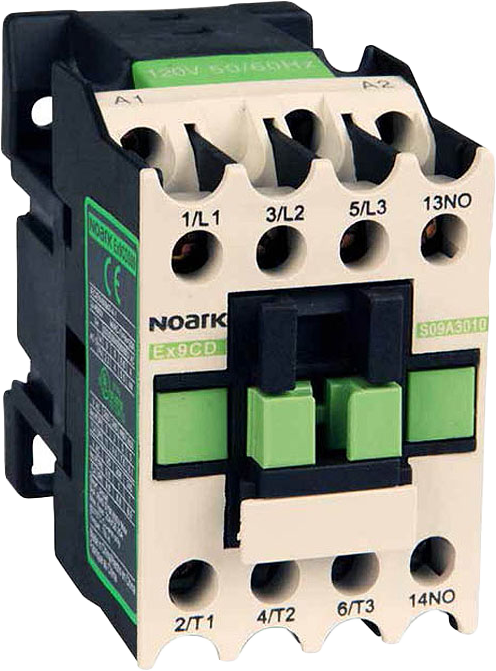
Overload Relays
To provide additional protection against overload, while allowing for minor voltage change, an overload relay is utilized.
These devices are comprised of a current-sensing unit connected to the motor input line, plus a mechanism controlled by the sensing unit which breaks the circuit during current overload. Built to tolerate the high inrush current during motor startup, overload relays have adjustable trip settings so they only trip when detecting what is designated as excess current flow. Additionally, overload relays are designed to either manually or automatically reset after tripping.
Where the contactor is the fast and generalized disconnect switching device, the overload relay is more finely tuned and will monitor the current only disconnecting during specified current ratings
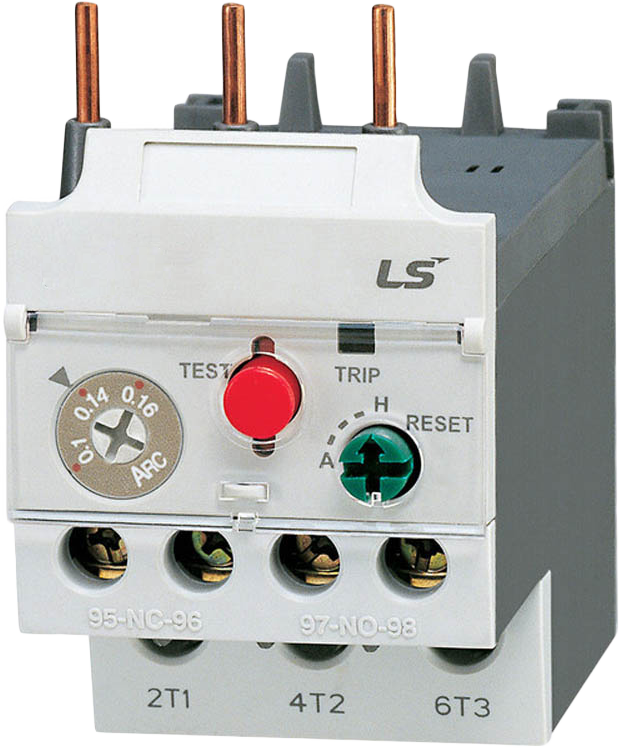
Manual Motor Starters (MMS)
Manual motor starters are the best of both worlds, combining the contactor and overload relay together for a more finely tuned product. Being manually operated, MMS are fitted with an ON/OFF button, toggle or rotary switch which, in certain designs, can be fitted with accessories allowing for operation on the panel interface.
This two-in-one option is ideal for panel mounting where space is limited, though this often means you’ll see a rise in cost.
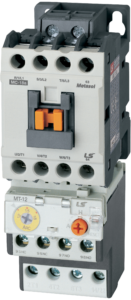
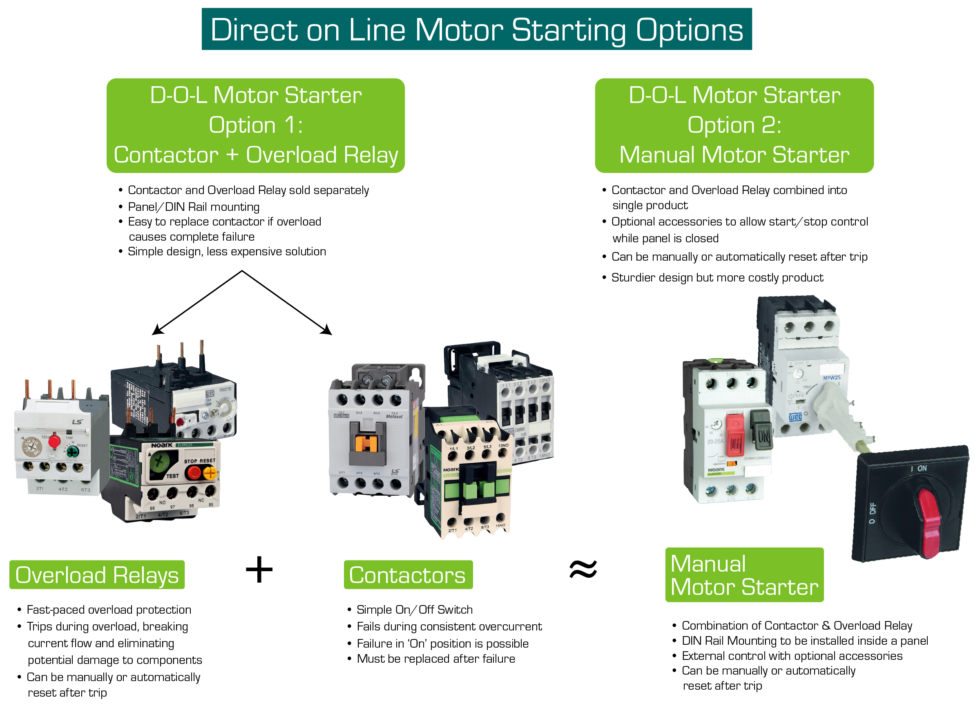
Pros and Cons of a DOL Starter
Not every project needs the most state-of-the-art starter to get the job done; keeping it simple can sometimes be the best option. Consider these pros and cons when deciding if DOL Starting is the right setup for your application:
Pros:
- Easy wiring setup and control, great for those who just want to plug and play
- Cost efficient solution
- Small motor rating, good for applications such as: small water pumps, blowers, packaging, fans, conveyor belts, and compressors
- Troubleshooting and part replacement is simple compared to other starting methods
- High torque is provided right at startup
Cons:
- High starting torque and voltage dips can easily damage equipment, this limits the recommended motor size
- Starting with unnecessarily high torque can reduce the overall lifespan of much of your equipment
- High starting torque can raise electrical costs with spikes in demand
If you’re looking for a quick and easy way to get your low HP induction motor wired and running, DOL startup is the perfect solution. Marshall Wolf Automation is your one-stop shop for contactors, overload relays and manual motor starters to get you going.
Want to learn more?
Looking for something a little more heavy duty? We’ve got tons of VFD, Rotary Phase Converters and Soft Stater options to learn about here:
Glossary:
- Contactor (aka ‘Mechanical Relay’): Simple On/Off switch with designated operating current. The simplistic mechanical design allows for longer lifespan compared to other devices but will need to be replaced in cases of overloading and failure. Comes in 3 options:
- Definite Purpose Contactor – used with lighting and HVAC applications
- IEC Contactor – used with motor applications
- NEMA Contactor – used with motor applications
- Combination Starter: See Manual Motor Starter
- Manual Motor Protector – MMP: See Manual Motor Starter
- Manual Motor Controller – MMC: See Manual Motor Starter
- Manual Motor Starter: (aka ‘Magnetic Starter,’ ‘Manual Motor Protector – MMP’, ‘Manual Motor Controller – MMC’, ‘Motor Starter/Starter’, ‘Motor Protection Circuit Breakers – MPCB’, and Combination Starter): A motor protection device which combines a circuit breaker and overload relays in order to protect the motor from overloading.
- Miniature Circuit Breaker – MCB: A more compact circuit breaker with low-voltage capacity which provides the same type of protection as a circuit breaker. Once an electrical overload crosses the MCB, it automatically trips ceasing any current flow.
- Molded Case Circuit Breaker – MCCB: Industrial circuit breakers break the electrical circuit during an overload and are part of the overall electrical safety system. Electrical industrial circuit breakers are automatically-operated switches to protect the electrical circuit from damage or potential fire.
- Motor Starter/Starter: See Manual Motor Starter
- Motor Protection Circuit Breakers – MPCB: See Manual Motor Starter
- Overload: Overload occurs when the motor is drawing excess current, potentially leading to overheating and damage to the motor or other components.
- Overload Relay (Solid State, Magnetic or Thermal Overload): Relays designed to protect AC circuits and motors against overloads, phase failure, long starting times and prolonged stalling of the motor. If the current rises above a certain limit over a period of time, the overload relay will trip, interrupting the motor control circuit and de-energizing the contactor. These can either be reset manually or in certain models, automatically reset.
- Resistive Load: A load whose total reactance is zero, so that the alternating current is in phase with the terminal voltage. Also known as ‘nonreactive load’.
For an even more in-depth look at DOL Motor Starters, check out this article from Electrical Engineering Portal or this insightful article from Electrical 4 U.